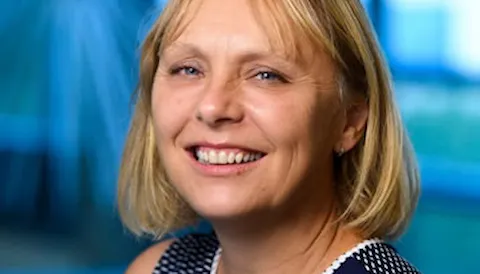
Views from the industry: RES
RES, the world’s largest independent renewable energy company, is active in wind, solar, energy storage, transmission and distribution. At the forefront of the industry, since it was founded in 1981, RES has delivered more than 17 GW of renewable energy projects across the globe and supports an operational asset portfolio exceeding 6 GW worldwide for a large client base.